
All number should be zero to be able to print as you can see it on the picture. Both of this will add a little box to the top-left of the window. You can enable the "Show non-manifold edges" and "Show non-manifold verticies" functions in the Render menu. Checking the second rule is a little bit harder, but not that much. Just open the model in MeshLab, and if it looks good, the first rule is probably okay. First of all, we need a software which can help detecting both of the above problems: we use MeshLab all the time to check the models. That was the theory, now let's see it in practice. These two rules guarantees the model will be water-proof, which means if we fill the inside up with water, the water will touch every polygon's inner side and there won't be any leak where the water can escape. This means every edge must connect to exactly two polygons. The model should be manifold, more precisely the model should be 2-manifold. The second problem is what we fought a lot in the past.
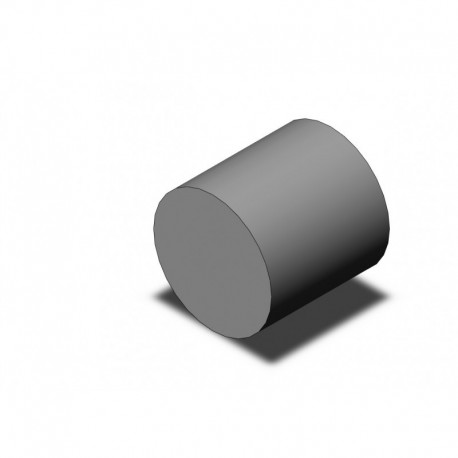
This doesn't cause too much trouble in printing, because this problem turns out much earlier, because this will affect the rendering as well. The first problem is that the polygons' normal must point to the outside.

This means the inside of the model is empty and the slicer needs to know somehow which part of the model should be filled. In the model there are a lot of polygons, which together looks like our object. This is not as simple as it looks at the first glance, because the model is not defined as a solid object.

And here's the trick: to slice the model, the slicer needs to know which is the outside and which is the inside. However this file cannot be printed directly, we need to slice it, which means we slice it to layers, and every layer consists of a lot of head movement which will result the model. Most 3D printer do this, because it is a pretty common file format. First of all, we use STL files as a source of a model. Before we start we need to talk about how the printing process looks like.
